Conquer Corrosion: The Ultimate Guide to Protecting Your Metal Structures in Florida
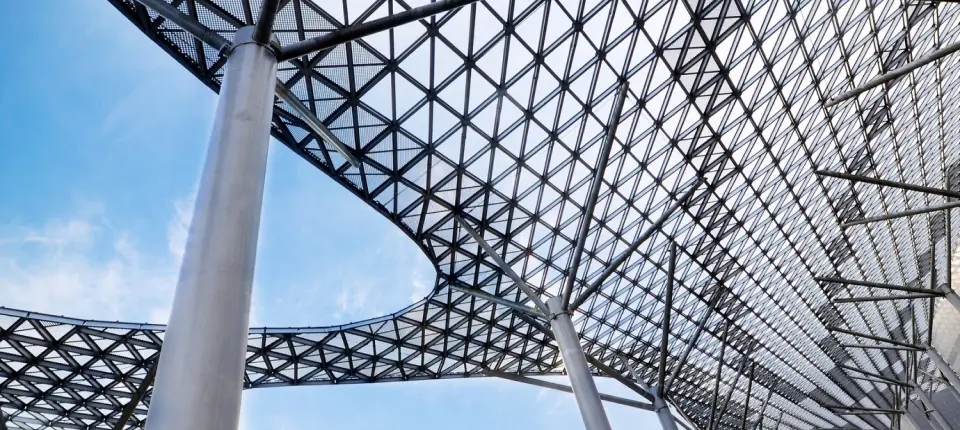
Florida’s climate isn’t just “challenging” for metal; it’s a relentless, corrosive onslaught. We’re talking about a constant barrage of high humidity, salt-laden air, intense ultraviolet radiation, and torrential rain – a perfect storm for metal degradation. Ignoring this reality is financially reckless. The annual cost of corrosion damage in coastal regions is staggering, and your property is directly exposed. The good news is that with the right knowledge, including the use of effective anti-corrosion metal coatings, you can significantly extend the life of your metal assets.
This guide provides the expert knowledge and strategies you need to decisively win the battle against metal deterioration, dramatically extending the life of your valuable metal assets. We’ll cover everything from preventative measures and cleaning techniques to material selection and smart repairs, all specifically tailored to Florida’s unique and demanding environment. Keep reading!
Understanding the Enemies: Corrosion Mechanisms in Florida
To effectively protect metal structures in Florida, it’s essential to understand the specific corrosion mechanisms at play. Corrosion isn’t a single, uniform process; it manifests in various forms, each driven by specific environmental factors and material interactions. Florida’s climate, with its high humidity, salt exposure, and intense sunlight, creates a particularly aggressive environment that accelerates these processes.
One of the most fundamental forms is general corrosion, also known as uniform corrosion. This is the relatively even, widespread attack you see as rust on steel or the patina that develops on copper. While seemingly slow, the constant presence of moisture in Florida’s humid air significantly speeds up this process, leading to gradual but consistent metal loss.
A more insidious threat is galvanic corrosion. This occurs when two dissimilar metals are in electrical contact within a conductive environment – a scenario readily provided by Florida’s salt-laden air and frequent rainfall. The more active (anodic) metal corrodes at an accelerated rate to protect the more noble (cathodic) metal. This often-overlooked phenomenon can lead to rapid and localized damage, especially where fasteners of one metal are used on a structure made of another. Think steel screws on an aluminum panel – a classic setup for galvanic corrosion.
Crevice corrosion exploits a different vulnerability: tight spaces. Wherever moisture can become trapped – under washers, between overlapping panels, in seams and joints – stagnant conditions develop. These confined areas become concentrated corrosion cells, leading to accelerated metal degradation, often hidden from view until significant damage has occurred.
Another highly damaging, localized form of corrosion is pitting corrosion. This manifests as small, deep pits that can penetrate metal surprisingly quickly. The insidious nature of pitting corrosion lies in its ability to remain largely undetected beneath a seemingly intact surface coating, making it a particularly dangerous threat.
Finally, we must consider microbiologically influenced corrosion (MIC). Florida’s warm, humid climate is a breeding ground for microorganisms like bacteria, fungi, and algae. Some of these organisms can directly contribute to corrosion by creating corrosive byproducts or even consuming metal as part of their metabolic processes. This adds another layer of complexity to the corrosion challenge in Florida.
Preventative Maintenance: Proactive Protection – Your First Line of Defense
The most effective, and ultimately most cost-effective, approach to corrosion is a proactive, preventative one. This requires a comprehensive strategy that addresses all potential vulnerabilities, from the initial selection of materials to ongoing maintenance practices.
Strategic Material Selection: The Foundation of Durability
Material selection is the crucial first step. The right material, chosen with Florida’s specific challenges in mind, will significantly reduce future maintenance needs and extend the lifespan of the structure. Aluminum, for example, offers inherent corrosion resistance. Marine-grade alloys like 5052 or 6061 are particularly well-suited for coastal environments. However, it’s important to be aware of potential galvanic corrosion when using aluminum with steel fasteners. Stainless steel is another excellent option, but grade selection is critical. In Florida’s coastal areas, 316 stainless steel, due to its higher molybdenum content, provides superior resistance to chloride attack compared to 304. Galvanized steel, with its protective zinc coating, offers a good level of protection. Keep in mind that the zinc layer is sacrificial and will eventually be depleted, requiring recoating or replacement. Hot-dip galvanizing provides a thicker, more durable coating than electro-galvanizing. Copper, while a more expensive option, forms a naturally protective patina and offers exceptional durability, making it a sound long-term investment, especially for roofing.
Avoiding Incompatible Metals: Preventing Electrochemical Reactions
Beyond the primary material choice, careful consideration must be given to how different metals interact. Whenever possible, use fasteners and other components made of the same material as the main structure. This eliminates the risk of galvanic corrosion, which occurs when dissimilar metals are in contact in a conductive environment. If different metals must be used, consult a galvanic series chart to determine compatibility and, crucially, use non-conductive materials like plastic washers or specialized isolating gaskets to prevent direct contact and electrical current flow.
Design for Drainage: Minimizing Moisture Accumulation
Proper structural design is also a key element of corrosion prevention. Ensuring adequate drainage on roofs, gutters, and all metal surfaces is essential. This prevents water from pooling, which creates conditions that significantly accelerate corrosion.
Protective Coatings: A Critical Barrier
Selecting the best metal coatings in Florida is crucial for protecting your investment from the harsh elements. Protective coatings provide a vital barrier between the metal and the corrosive environment. Selecting the appropriate coating system and ensuring its proper application is essential. For paints, consider the specific performance characteristics of different types. Epoxy paints offer excellent adhesion and chemical resistance, making them suitable for harsh environments. Polyurethane paints provide high UV resistance and abrasion resistance, making them ideal for exterior applications exposed to sunlight. Acrylic paints, being more flexible, are a good choice for areas subject to temperature fluctuations. However, regardless of the paint type, proper surface preparation is paramount. Thorough cleaning, rust removal, and priming are essential for achieving long-term coating performance. Powder coatings, applied in a factory setting and baked on, offer superior durability and resistance to UV radiation, scratches, and chemicals, making them an excellent choice for new metal components. In addition to paints and powder coatings, high-quality, UV-resistant sealants, specifically formulated for metal, are crucial for sealing joints, seams, and around fasteners. This prevents water intrusion and minimizes the risk of crevice corrosion. Wax-based or oil-based protectants offer an additional option for enhancing water repellency.
Regular Inspections: Early Detection and Prevention
Regular inspections are a critical part of any effective maintenance program. Establish a consistent inspection schedule – at least annually, and after any major storms. During inspections, look for any signs of corrosion, such as rust spots, bubbling or peeling paint, discoloration, or chalking. Check fasteners for looseness, corrosion, or missing parts. Inspect for any cracks, dents, or other physical damage. Pay close attention to areas where water might collect, and carefully examine any locations where different metals are in contact. Assess the condition of sealants, checking for cracks, peeling, or gaps.
Landscaping and Irrigation: Controlling Environmental Factors
Even surrounding landscaping and irrigation systems can influence corrosion rates. Overhanging vegetation should be trimmed to prevent branches from scratching coatings, leaves from trapping moisture, and falling debris from causing damage. Irrigation systems should be positioned and adjusted to avoid direct sprinkler spray on metal surfaces, as the constant wetting and drying cycles accelerate corrosion.
Proper Fastener Selection and Installation: Attention to Detail
The choice and installation of fasteners are often overlooked but critical details. Avoid galvanic corrosion by using fasteners made of the same material as the structure, or a compatible material. Select fasteners with superior corrosion resistance, such as those that are hot-dip galvanized or feature specialized protective coatings. And, ensure proper installation by avoiding both over-torquing and under-torquing, which can compromise the fastener’s integrity and create entry points for moisture.
Cleaning Metal Structures: Essential Maintenance
Regular cleaning is not merely about aesthetics; it’s an integral part of preventative maintenance for metal structures in Florida’s challenging climate. Cleaning removes corrosive contaminants, like salt deposits, dirt, and biological growth, and allows for a closer inspection of the metal’s surface.
General Cleaning Practices
A general cleaning should be performed every six to twelve months, or more frequently in coastal areas or after exposure to significant weather events. For routine cleaning to remove general dirt and grime, a solution of mild dish soap and water is often sufficient. Pressure washing can be a useful tool, but it must be employed with caution. Use a low-pressure setting and a wide-angle nozzle to avoid damaging coatings or forcing water into crevices and seams. Never use high pressure on painted metal surfaces. For more stubborn stains or accumulated deposits, consider using a cleaner specifically formulated for the type of metal you are cleaning. Always test any specialized cleaner in an inconspicuous area first to ensure it doesn’t damage the finish.
Addressing Mildew and Algae Growth
Mildew and algae, common in Florida’s humid environment, are more than just unsightly; they trap moisture against the metal surface, creating ideal conditions for corrosion. To remove these biological growths, a diluted bleach solution can be effective (always follow the manufacturer’s instructions and wear appropriate safety gear, including gloves and eye protection). Alternatively, commercial mildewcides designed for exterior use are available. Regardless of the cleaning solution used, thorough rinsing with fresh water after application is absolutely crucial to remove any residual chemicals.
The Importance of Salt Removal
In coastal areas, salt deposits are a constant and highly corrosive threat. Regular removal of salt is essential to prevent accelerated corrosion. Frequent rinsing with fresh water, particularly after storms or exposure to salt spray, is the primary defense. For persistent salt buildup, consider using a specialized salt-removing product designed for use on metal surfaces. These products are formulated to effectively dissolve and neutralize salt deposits without harming the underlying metal or coating.
Repair and Remediation: Addressing Inevitable Issues
Even with the most diligent preventative maintenance, some degree of wear and tear, or even corrosion, is likely to occur over time, especially in Florida’s harsh environment. Prompt and appropriate repair is crucial to prevent minor issues from escalating into major problems.
Addressing Rust: From Minor to Major
Rust, the most common form of corrosion on steel, requires immediate attention. For small, isolated rust spots, the solution can be relatively straightforward. Thoroughly remove the rust by wire brushing or sanding the affected area down to bare metal. Following rust removal, apply a rust converter to neutralize any remaining corrosion and create a stable surface for coating. Finally, prime and repaint the area with a coating system compatible with the existing finish. However, extensive rust indicates a more serious underlying problem, potentially compromising the structural integrity of the metal. In such cases, professional assessment and repair are strongly recommended. This may involve welding, patching, or even replacement of the affected section. Delaying action on extensive rust will only lead to more costly and complex repairs down the line.
Repairing Damaged Coatings: Restoring the Protective Barrier
Coatings are the first line of defense against corrosion, so maintaining their integrity is essential. For minor scratches and chips, a simple touch-up may suffice. Clean the damaged area thoroughly, and apply a touch-up primer and paint that matches the existing coating, ensuring proper feathering of the edges for a seamless repair. Larger areas of coating damage require a more involved approach. Carefully feather the edges of the damaged area to create a smooth transition, clean the entire area thoroughly, apply an appropriate primer, and then recoat with a compatible paint system, following the manufacturer’s recommendations for application and drying times.
Replacing Damaged Components: Addressing Structural Issues
When damage extends beyond the coating to the underlying metal components, replacement may be necessary. Corroded or damaged fasteners should be replaced with identical or compatible replacements, paying close attention to material compatibility to avoid creating new galvanic corrosion issues. For severely damaged structural components, such as panels or sections of a metal building, consulting a qualified contractor is essential. They can properly assess the extent of the damage and perform the necessary repairs or replacements to restore the structural integrity and safety of the structure.
Addressing Galvanic Corrosion
Dealing with galvanic corrosion requires identifying and isolating the dissimilar metals involved. Introducing non-conductive materials, like plastic washers or specialized gaskets, between the metals can effectively break the electrical circuit. Applying protective coatings to one or both metals can also serve as a barrier, preventing the electrochemical reaction.
Special Considerations for Marine Environments: The Extreme Zone
Properties located near the coast face an even greater corrosion challenge. In these environments, increased maintenance frequency is paramount. Inspect and clean metal structures more often than you would inland. For submerged metal structures, such as docks or boat lifts, consider the use of sacrificial anodes. These anodes, typically made of zinc or magnesium, corrode preferentially, protecting the more valuable metal components.
Protect Your Investment with C & R Metals
Don’t let Florida’s climate win. For all your metal needs, turn to C & R Metals, your trusted metal supply Miami source. With over 40 years of experience serving South Florida, we provide a comprehensive range of high-quality metal products, including any type of metal you require, along with a complete selection of fasteners and the specialized paints you need for lasting protection.
But we’re more than just a supplier. We offer exceptional services to meet your exact specifications, including custom fabrication, precision waterjet cutting, and expert welding.
Visit C & R Metals at 2991 NW North River Dr., Miami, FL, 33142 today and let our experienced team help you protect your metal structures for years to come!
Conclusion
This guide has covered a lot of ground, from understanding the specific types of corrosion that thrive in Florida’s climate to implementing detailed preventative maintenance, cleaning, and repair strategies. We’ve emphasized the importance of material selection, the dangers of galvanic corrosion, the necessity of protective coatings, and the critical role of regular inspections and cleaning. We also highlighted how seemingly minor details, like fastener choice and landscaping, can significantly impact the longevity of your metal structures. Ultimately, protecting your metal investments in Florida requires a proactive, informed approach.
Need metal, fasteners, anti-corrosion coatings, or fabrication in Miami? C & R Metals, your trusted metal supply Miami source, has you covered. Call us now: (305) 634-2111.
Key Takeaways
- Regular inspections, cleaning, and timely maintenance will significantly extend the lifespan of your metal structures and save you money in the long run.
- Choosing the right metal for the Florida environment and using high-quality, appropriate coatings form the foundation of corrosion resistance.
- Knowing the signs of galvanic corrosion, crevice corrosion, and pitting corrosion allows for targeted interventions before significant damage occurs.