An Expert Guide to Aluminum Grades
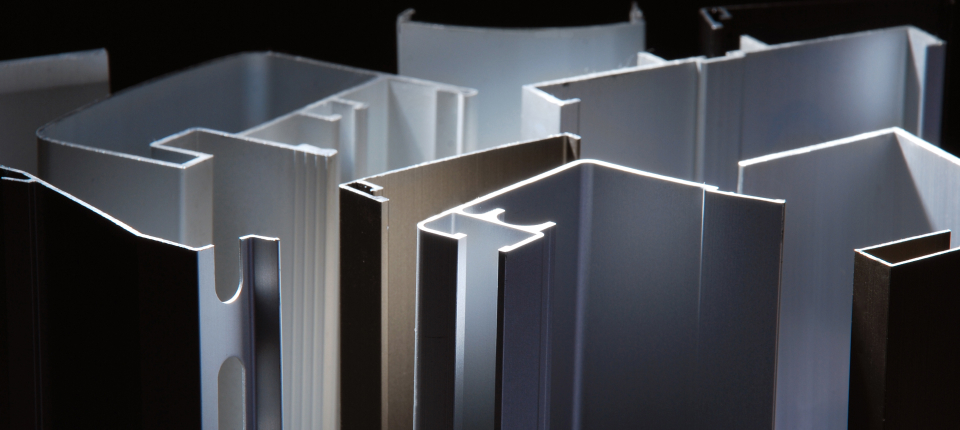
Aluminum is a versatile metal with a wide range of applications across numerous industries, from aerospace and automotive to construction and consumer goods. Its lightweight nature, high strength-to-weight ratio, corrosion resistance, and recyclability make it a popular choice for various products. The use of aluminum for commercial projects is increasingly prevalent due to its durability, aesthetic appeal, and design flexibility. However, not all aluminum is created equal. Different aluminum grades offer unique properties and characteristics that make them suitable for specific applications. This guide provides a comprehensive overview of aluminum grades, their properties, and their uses.
Understanding Aluminum Grades
Aluminum alloys are classified into series based on their primary alloying elements. The Aluminum Association Inc. designates wrought aluminum alloys with a four-digit number, where the first digit indicates the alloying element.
1xxx Series
This series comprises alloys with a minimum aluminum content of 99%, often referred to as “commercially pure aluminum.” They are known for outstanding corrosion resistance, superior electrical and thermal conductivity, and excellent workability. However, they have low mechanical strength and are not heat-treatable. Common impurities in this series include iron (Fe) and silicon (Si).
2xxx Series
Copper is the primary alloying element in this series. These alloys offer high strength and good machinability but have lower corrosion resistance. They are often used in the aerospace industry for components like aircraft structures and skins due to their excellent toughness and hardness when heat-treated.
3xxx Series
These alloys primarily contain manganese. They are suitable for general purpose uses and are among the most popular choices. They have moderate strength, good corrosion resistance, and good workability. The addition of manganese increases strength while maintaining ductility and corrosion resistance8. This series includes 3003, one of the most widely used aluminum alloys, known for its versatility and excellent weldability.
4xxx Series
Silicon is the primary alloying element in this series. They are used to lower the melting point of the material while keeping its ductility. Alloy 4043 is a popular choice for welding wire, suitable for use in elevated temperatures and offering a smoother finish. The 4000 series generally offers good thermal and electrical conductivity and good corrosion resistance, making these alloys popular in automotive engineering.
5xxx Series
These alloys are primarily combined with magnesium, but many contain additional elements such as manganese or chromium. Magnesium significantly improves corrosion resistance, especially in marine environments, making them popular for marine applications such as boat hulls, storage tanks, pressure valves, and cryogenic tanks. These versatile alloys maintain moderate strength, weldability, and respond well to working and forming. Another commonly used welding wire is made from Alloy 5356, often chosen for aesthetic purposes as it keeps its color after anodizing.
6xxx Series
These alloys combine magnesium and silicon, forming magnesium silicide. They are extremely common for general-purpose uses in various industries, including construction, architecture, and automotive. With above-average strength, strong corrosion resistance, and good machinability, these alloys respond well to heat treatment and maintain their workability after tempering or annealing. One of the most popular alloys for the UK market is 6082, available in several profiles, including sheet, box section, bars, I-beam, and channel. If you are searching for aluminum sheets in Miami, this series, particularly in readily available forms, is a great place to start your search.
7xxx Series
Zinc is the primary alloying element in this series. They offer very high strength, good fatigue resistance, and moderate corrosion resistance. Heat treatment can further increase their strength.
8xxx Series
This series includes other elements as primary alloying elements, such as lithium, tin, and iron.
Key Properties of Aluminum Grades
Each aluminum grade has unique properties that make it suitable for specific applications. Some of the key properties include:
Strength
The ability to withstand stress without permanent deformation or fracture. Tensile strength and yield strength are common measures of strength. High strength is crucial for aerospace and structural applications.
Corrosion Resistance
Aluminum alloys are naturally corrosion-resistant due to the formation of a protective oxide layer. Different grades offer varying levels of resistance depending on their alloying elements and environment. Good corrosion resistance is essential for marine and outdoor applications.
Workability
The ease with which aluminum can be formed, shaped, or machined. Some grades are more ductile and malleable than others, making them suitable for intricate designs.
Weldability
The ability of aluminum to be welded without creating defects or weakening the material. Some grades are more weldable than others.
Machinability
The ease with which aluminum can be machined or cut. Some grades are more machinable than others, producing better surface finishes and requiring less tooling wear.
Heat Treatability
Some aluminum grades can be heat-treated to enhance their properties, such as strength and hardness. Heat treatment involves heating the aluminum to a specific temperature and then cooling it at a controlled rate.
Common Aluminum Grades and Their Applications
While numerous aluminum grades exist, some are more common in the US market due to their versatility and suitability for various applications. These include:
1100
This is commercially pure aluminum with excellent corrosion resistance, workability, and electrical conductivity. It is commonly used for chemical equipment, fin stock, and general fabrication.
2024
A high-strength alloy with good fatigue resistance, commonly used in aerospace applications, particularly for aircraft structures.
3003
This is the most widely used aluminum alloy and a general-purpose alloy. It offers moderate strength, good corrosion resistance, and excellent workability. It is commonly used for cooking utensils and general sheet metal work.
5052
This is the strongest non-heat-treatable alloy with excellent corrosion resistance, particularly in marine environments. It is commonly used for marine applications, such as boat hulls and electronic components.
6061
This is a versatile heat-treatable alloy with a good balance of strength, corrosion resistance, and workability. It is widely used in structural applications, general fabrication, and automotive parts.
6063
This is commonly known as the “architectural alloy” due to its excellent finishing characteristics and corrosion resistance. It is often used for architectural applications, such as window and door frames.
7075
This is one of the highest strength aluminum alloys with an excellent strength-to-weight ratio. It is commonly used in aerospace applications, high-performance sporting goods, and tooling.
Cast vs. Wrought Aluminum
Aluminum alloys are also categorized as either cast or wrought. Wrought aluminum is shaped by mechanical processes such as rolling, extrusion, and forging, while cast aluminum is produced by melting the metal and pouring it into a mold. Wrought aluminum generally offers higher mechanical strength, excellent corrosion resistance, good formability, and weldability. Cast aluminum, on the other hand, has lower tensile strength but is known for its excellent machinability, allowing for intricate designs and precise tolerances.
Choosing the Right Aluminum Grade
Selecting the appropriate aluminum grade depends on several factors, including:
Application Requirements
The intended use of the aluminum component dictates the necessary properties. For example, aircraft parts require high strength and fatigue resistance (like 2024 or 7075), while cooking utensils need good workability and corrosion resistance (like 3003). Determining the best aluminum grade for construction projects often involves considering factors like structural load, environmental exposure, and desired aesthetic finish. Alloys like 6061 and 6063 are frequently chosen due to their balance of strength, corrosion resistance, and weldability.
Strength-to-Weight Ratio
When weight is a concern, high-strength alloys like those in the 2xxx and 7xxx series are preferred. These alloys are commonly used in aerospace and transportation applications where lightweight and strong components are crucial.
Corrosion Resistance
For marine or outdoor applications, alloys with excellent corrosion resistance, such as those in the 1xxx, 3xxx, and 5xxx series, are essential. These alloys form a protective oxide layer that prevents corrosion, making them suitable for harsh environments.
Machinability
If the component requires intricate machining, alloys with good machinability, like those in the 2xxx and 6xxx series, are preferred. These alloys can be easily cut and shaped with standard tooling, resulting in better surface finishes and less tool wear.
Heat Treatment
If enhanced properties are required, heat-treatable alloys like those in the 2xxx, 6xxx, and 7xxx series can be considered. Heat treatment processes can increase strength, hardness, and other mechanical properties.
Weldability
For applications requiring welding, alloys with good weldability, such as those in the 1xxx, 3xxx, and 5xxx series, are preferred. These alloys can be easily welded without creating defects or compromising the material’s strength.
Conclusion
We’ve explored the diverse world of aluminum grades, highlighting their unique properties, classifications, and applications. From the commercially pure 1xxx series to the high-strength 7xxx series, each grade offers specific characteristics that make it suitable for particular uses, whether it’s the corrosion resistance of 5052 in marine environments or the structural integrity of 6061 in construction. We’ve touched upon key factors such as strength, corrosion resistance, workability, weldability and machinability. Understanding these differences is crucial for selecting the right material for your project, ensuring optimal performance and longevity.
Ready to put this knowledge into action? Look no further than C & R Metals, your trustworthy metal supplier and hardware store in Miami. We offer a comprehensive selection of aluminum grades to meet any requirement. Moreover, we offer custom aluminum fabrication services. Our expertise spans everything from sturdy structural components to intricate decorative pieces – tell us your vision, and we’ll make it a reality. Contact C & R Metals at (305) 634-2111 today and let us help you with any of your projects!
Key Takeaways
- Different aluminum grades (designated by a numbering system) possess unique properties like strength, corrosion resistance, and workability, making them suitable for specific applications.
- Choosing the right aluminum grade depends on factors such as application requirements, strength-to-weight ratio, corrosion resistance needs, machinability, heat treatability, and weldability.
- Common aluminum alloys like 3003, 5052, 6061, and 6063 are widely used across various industries, including construction, marine applications, and commercial projects.