What Makes Plasma Cutting Ideal for Steel and Stainless Steel
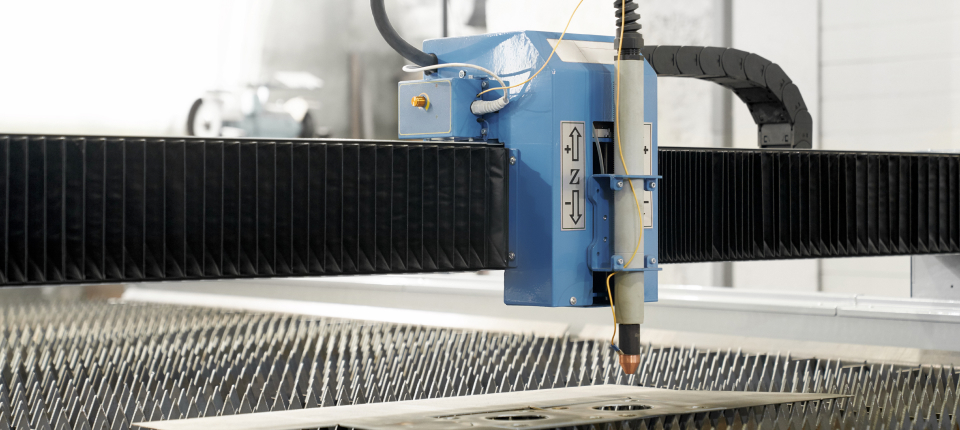
In the world of metal fabrication, choosing the right cutting process is paramount. It dictates efficiency, precision, and ultimately, the quality of the final product. While various methods exist, plasma arc cutting consistently emerges as a remarkably effective solution, particularly when working with two of the most common and versatile materials: steel and stainless steel. Its widespread adoption isn’t accidental; it stems from a confluence of physics, performance characteristics, and practical advantages that make it uniquely suited for these ferrous metals. Understanding these benefits of plasma cutting in metal fabrication, particularly why plasma excels with steel, unlocks greater potential in design and production.
The Fundamental Power: Harnessing Ionized Gas
At its core, plasma cutting operates on a principle that feels almost futuristic, yet is elegantly simple in concept. It involves creating an extremely high-temperature, electrically conductive channel of ionized gas – the plasma itself – between an electrode within the plasma torch and the workpiece (the steel). This isn’t merely heat; it’s a focused jet of superheated matter, typically reaching temperatures exceeding 20,000°C (36,000°F). This intense energy instantly melts the metal it contacts. Simultaneously, a high-velocity flow of gas (often compressed air, nitrogen, oxygen, or specific mixtures depending on the material and desired cut quality) blasts this molten metal away, creating the kerf, or cut path. The process relies fundamentally on the material being cut having sufficient electrical conductivity to complete the circuit and sustain the arc.
Steel’s Natural Partnership: Electrical Conductivity
This brings us directly to the first major reason plasma is so well-suited for steel and its stainless counterpart: their inherent electrical conductivity. Both mild steel and various grades of stainless steel are excellent conductors of electricity. This property is non-negotiable for plasma cutting to function effectively in its most common transferred arc configuration. The electrical arc must readily establish itself between the torch electrode and the steel plate or sheet. Without this conductive pathway, the intense energy required for melting cannot be efficiently delivered to the precise point of the cut. Metals that are poor conductors pose significant challenges for standard plasma cutting setups. Steel, however, offers a reliable path for the current, enabling a stable, powerful arc that translates directly into efficient cutting action. This fundamental compatibility is the bedrock upon which plasma’s success with steel is built.
Unleashing Speed: The Productivity Engine
One of the most compelling advantages of plasma cutting for steel is its impressive cutting speed, especially when compared to mechanical methods like sawing or drilling for complex shapes, or even oxy-fuel cutting on thinner to medium-thickness materials. The sheer thermal energy concentrated in the plasma arc melts steel almost instantaneously upon contact. Coupled with the high-velocity gas jet clearing the molten material, the torch can traverse the metal at remarkable rates. On thinner gauge steel sheets, plasma cutting can be significantly faster than many alternatives, dramatically reducing processing time per part. Even on thicker plates, while speeds naturally decrease, plasma often maintains a significant throughput advantage over methods requiring preheating or slower mechanical action. This speed translates directly into increased productivity and potentially lower labor costs per cut, a critical factor in any production environment. Modern CNC plasma systems further leverage this speed, executing complex cutting programs with rapidity and precision that manual methods cannot match.
Tackling Thickness: Versatility Across Gauges
Plasma cutting isn’t a one-trick pony limited to thin materials. Its capabilities extend across a substantial range of steel thicknesses. While laser cutting might dominate ultra-thin sheet metal applications demanding the absolute finest edge quality, plasma truly shines in its versatility from relatively thin gauge material (say, 1mm or less) up to very thick plates (often 50mm / 2 inches, and sometimes significantly more with high-amperage industrial systems). Handheld units offer portability for thinner to moderate tasks, while robust CNC gantry systems equipped with powerful plasma sources can confidently sever thick structural steel sections. This adaptability means a single plasma system can potentially handle a vast spectrum of project requirements, from intricate sheet metal designs to heavy plate profiling. This ability to effectively address both thin and thick steel sections with the same core technology minimizes the need for multiple, disparate cutting processes within a workshop, streamlining workflow and equipment investment.
Mastering Geometry: Freedom in Design
The nature of the plasma arc – a focused, directional cutting tool – grants exceptional freedom in creating complex shapes and profiles in steel. Unlike mechanical methods like shearing (limited to straight lines) or sawing (often restricted by blade access and radius), plasma can follow intricate paths, curves, sharp corners, and internal cutouts with relative ease, especially when guided by a CNC controller. This allows designers and fabricators to move beyond simple geometric constraints and realize more complex and aesthetically demanding designs in steel plate and sheet. Bevel cuts for weld preparation can also be achieved with specialized torch heads or multi-axis CNC systems. This geometric flexibility is invaluable for applications ranging from custom signage and artistic metalwork to precisely shaped components for machinery and structural assemblies. The plasma torch doesn’t bind or deflect easily like a mechanical blade can, enabling consistent accuracy even on non-linear cut paths through tough steel materials.
The Stainless Steel Solution: Overcoming Oxidation Challenges
Stainless steel presents a unique challenge for thermal cutting methods that rely on oxidation, primarily oxy-fuel cutting. Oxy-fuel works exceptionally well on carbon steel because the iron readily oxidizes (burns) in the presence of pure oxygen, creating an exothermic reaction that sustains the cut. Stainless steel, however, contains significant amounts of chromium, which forms a tenacious, passive chromium oxide layer on the surface. This layer inhibits the rapid oxidation necessary for the oxy-fuel process to work effectively. Attempting to cut stainless steel with oxy-fuel typically results in a messy, incomplete cut with excessive slag and poor edge quality. Evaluating Plasma cutting vs. other methods for stainless steel highlights plasma’s advantage here, as it elegantly sidesteps this issue. Because plasma relies on melting the material rather than burning it through oxidation, the chromium content of stainless steel is not an impediment. The intense heat of the plasma arc simply melts the stainless steel, and the high-velocity gas jet blows the molten material away. Specific gas mixtures, often involving nitrogen or argon/hydrogen blends, are frequently used when cutting stainless steel with plasma to achieve optimal edge quality, minimize discoloration (oxidation staining near the cut edge), and ensure good dross control. This makes plasma the go-to thermal cutting process for achieving clean, fast cuts on a wide range of stainless steel grades and thicknesses.
Edge Quality and the Heat Affected Zone (HAZ)
While perhaps not achieving the near-mirror finish of a fiber laser on thin stainless steel, modern high-definition plasma systems deliver excellent cut quality on both steel and stainless steel, characterized by a relatively smooth edge, minimal dross (resolidified metal clinging to the bottom edge), and good squareness. The quality achievable often reduces or eliminates the need for secondary grinding or finishing operations, saving time and labor. Equally important is the Heat Affected Zone (HAZ). Any thermal cutting process introduces heat into the material adjacent to the cut line, potentially altering its microstructure and properties. Because plasma cutting is typically very fast, the heat input is concentrated over a shorter duration compared to slower processes like oxy-fuel, especially on thicker materials where oxy-fuel requires significant preheating. This generally results in a narrower HAZ with plasma cutting. Minimizing the HAZ is crucial for maintaining the desired mechanical properties (like hardness and toughness) and corrosion resistance (particularly important for stainless steel) of the material near the cut edge. While some HAZ is unavoidable, plasma often represents a favorable balance between cutting speed, versatility, and controlled thermal impact on steel and stainless steel.
Cost-Effectiveness in Practice
When considering the entire fabrication workflow, plasma cutting presents a highly cost-effective solution for processing steel and stainless steel. The initial investment for plasma systems can vary significantly, from affordable handheld units to sophisticated industrial CNC tables. However, the operational costs are often favorable. Plasma cutting typically doesn’t require the expensive consumable gases associated with laser (though cutting gases are used) and avoids the significant preheating times and oxygen consumption inherent in oxy-fuel cutting of thicker steel. The high cutting speeds directly reduce labor hours per part. The versatility across thicknesses and materials can reduce the need for multiple cutting stations. Furthermore, the good edge quality achievable can minimize downstream processing costs associated with grinding or edge finishing. When viewed holistically – considering equipment cost, consumables, labor, speed, versatility, and secondary processing needs – plasma frequently emerges as an economically advantageous choice for a vast range of steel and stainless steel cutting applications.
The Synergistic Choice
The suitability of plasma cutting for steel and stainless steel is not down to a single factor, but rather a powerful synergy between the process physics and the material properties. The essential electrical conductivity of steel enables the arc. The intense, focused heat efficiently melts these robust metals. The high-velocity gas effectively clears the kerf. This combination delivers exceptional speed across various thicknesses and allows for intricate geometric freedom. Crucially for stainless steel, plasma overcomes the oxidation barrier that hinders oxy-fuel, providing a clean and efficient melting-based solution. The resulting good edge quality, manageable HAZ, and overall cost-effectiveness solidify plasma’s position as an ideal, practical, and powerful tool for anyone shaping steel and stainless steel. Understanding these underlying reasons empowers better decision-making in fabrication, ensuring the right process is chosen to unlock the full potential of these indispensable materials.
Concluision
The exceptional suitability of plasma arc cutting for steel and stainless steel is clearly no accident. Its power stems from the fundamental electrical conductivity inherent in these metals, enabling rapid, localized melting via the intensely focused plasma arc. This synergy translates directly into tangible benefits explored throughout this discussion: significant gains in processing speed that drive productivity, remarkable versatility across a wide spectrum of material thicknesses, and the crucial capability to execute intricate geometric designs with high fidelity. Critically, especially for stainless grades, plasma cutting cleanly bypasses the oxidation challenges that hinder other thermal methods, delivering superior results. When combined with generally favorable edge quality, a minimized heat-affected zone compared to some alternatives, and overall operational cost-effectiveness, plasma solidifies its role as a powerhouse technology in modern metal fabrication.
Understanding these principles and leveraging this technology is central to the service we provide at C & R Metals. As one of the premier stainless steel suppliers in Florida, we recognize that having the right material is only part of the equation. That’s why we not only ensure we have whatever metal you need in stock but also offer precision plasma cutting services tailored to your project’s demands. We routinely handle both steel and stainless steel plate, confidently processing thicknesses ranging from 1/8” up to 2” – and even thicker materials for specific requirements. Our goal is to provide comprehensive solutions, transforming raw stock into precisely cut components ready for your fabrication process. Leverage our material inventory and advanced plasma cutting capabilities; contact C & R Metals at (305) 634-2111 to discuss how we can supply and process the steel or stainless steel for your next project, ensuring efficiency and quality from start to finish.
Key Takeaways
- Plasma cutting leverages the inherent electrical conductivity of steel and stainless steel to create a high-energy arc that rapidly melts the material.
- This process delivers significant advantages in cutting speed, the ability to handle diverse material thicknesses, and the flexibility to create complex shapes.
- Plasma effectively cuts stainless steel through melting, overcoming the oxidation limitations faced by methods like oxy-fuel cutting.