A Beginner’s Guide to Choosing Fasteners and Hardware for Metal Projects
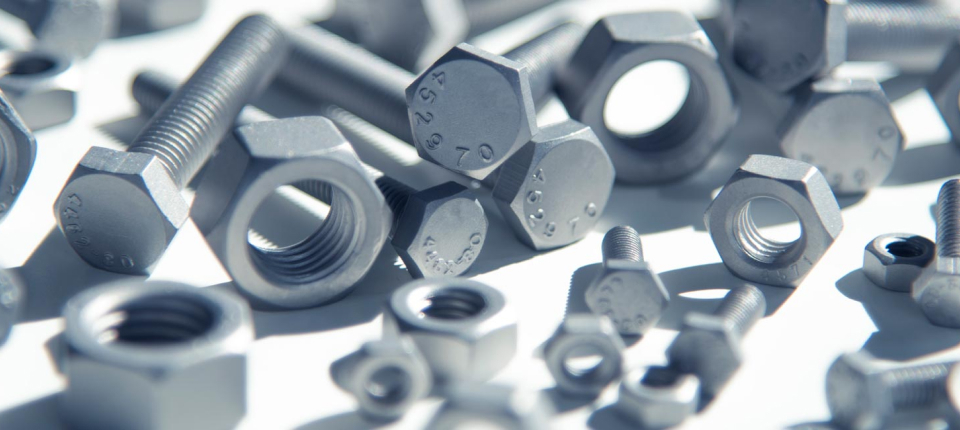
In metalworking, the strength and longevity of your projects depend not only on the quality of the metal itself but also on the often-overlooked components that hold it all together: fasteners and hardware. Don’t make the mistake of treating these small but crucial elements as an afterthought. Choosing the wrong screws, bolts, or nuts can lead to weak joints, structural instability, and even project failure. This comprehensive guide will equip you with the knowledge to confidently navigate the world of hardware and fasteners in South Florida, ensuring your metalworking projects are built to last.
Understanding the Basics: Types of Fasteners
Before visiting a fastener supplier and diving into the selection process, it’s essential to familiarize yourself with the diverse world of fasteners. Each type of fastener serves a specific purpose and exhibits unique characteristics that influence its suitability for different applications.
Screws
Perhaps the most ubiquitous fastener, screws come in a vast array of shapes, sizes, and materials. They typically feature a helical thread that engages with a corresponding threaded hole or nut, creating a secure clamping force. Screws are versatile and can be used for joining various materials, including metal, wood, and plastic.
Bolts
Bolts are similar to screws but are typically larger and designed to be used with nuts. They often feature a head with a specific drive type (e.g., hex, Torx) for tightening. Bolts are commonly used in structural applications requiring high strength and clamping force.
Nuts
Nuts are threaded components that mate with bolts to create a secure joint. They come in various shapes, including hex, square, and wing nuts, each with its own advantages and applications. Nuts distribute the clamping force over a larger area, preventing damage to the joined materials.
Washers
Washers are thin, flat components typically used in conjunction with screws and bolts. They distribute the load of the fastener, preventing damage to the material surface and providing a more secure grip. Washers also help to prevent loosening and vibration.
Rivets
Rivets are permanent fasteners that are used to join two or more pieces of material. They consist of a cylindrical shaft with a head on one end. The rivet is inserted through holes in the materials to be joined, and headless end is deformed to create a second head, securing the joint. Rivets are commonly used in applications where disassembly is not required, such as in aircraft construction and structural steelwork.
Material Matters: Selecting the Right Metal
The choice of material for your fasteners and hardware is crucial, as it directly impacts their strength, corrosion resistance, and overall performance. When evaluating your options from a metal supply, consider the specific demands of your project and the environment in which the fasteners will be used.
Steel
Steel is a versatile and widely used material for fasteners due to its high strength and affordability. Carbon steel fasteners are suitable for general-purpose applications, while alloy steels offer enhanced properties such as increased strength, toughness, or corrosion resistance. Stainless steel fasteners are ideal for applications requiring high corrosion resistance, such as marine environments or outdoor projects.
Aluminum
Aluminum fasteners are lightweight and corrosion-resistant, making them suitable for applications where weight is a concern, such as in aerospace and automotive industries. However, aluminum fasteners generally have lower strength compared to steel fasteners.
Brass and Bronze
Brass and bronze fasteners offer a combination of strength, corrosion resistance, and aesthetic appeal. They are often used in decorative hardware, marine applications, and plumbing fixtures.
Titanium
Titanium fasteners are prized for their exceptional strength-to-weight ratio, corrosion resistance, and biocompatibility. They are commonly used in aerospace, medical implants, and high-performance applications where weight and strength are critical factors.
Zinc
With its relatively low melting point and good corrosion resistance, zinc is often used as a coating for steel fasteners to provide galvanic protection. This process, known as galvanization, creates a sacrificial layer of zinc that corrodes preferentially to the underlying steel, extending the lifespan of the fastener. Zinc alloys, such as Zamak, are also used for die-cast fasteners due to their good castability and dimensional stability. These zinc fasteners are commonly found in automotive components, hardware, and consumer products.
Understanding Fastener Grades and Classes
Just as with the metals themselves, fasteners are also categorized into different grades and classes to ensure standardization and provide a clear indication of their mechanical properties. These grades and classes are typically designated by markings on the fastener head, providing valuable information about their strength, durability, and suitability for various applications. These standards are defined by organizations like ASTM International (formerly known as the American Society for Testing and Materials) and the Society of Automotive Engineers (SAE). ASTM standards, such as ASTM A325 for structural bolts, provide detailed specifications for material properties, dimensions, and testing procedures.
Steel Fastener Grades
Steel fasteners, particularly bolts, are commonly graded according to their tensile strength and yield strength. These grades are often represented by a series of markings on the bolt head. For example, a bolt with the marking “8.8” indicates a minimum tensile strength of 800 MPa and a minimum yield strength of 640 MPa (80% of the tensile strength). Higher grade numbers indicate higher strength. Other common steel fastener grades include 9.8, 10.9, and 12.9, each with increasing strength capabilities. The highest grade commonly available is 12.9, offering exceptional tensile strength and hardness.
Can you use a bolt with a lower grade instead of a higher grade? While it might be tempting to substitute a lower-grade bolt to save on cost, it’s crucial to prioritize safety and performance. Using a lower-grade bolt than specified can compromise the structural integrity of your project and potentially lead to failure. Always adhere to the recommended grade or consult with a qualified engineer if you have any doubts.
Stainless Steel Fastener Classes
Stainless steel fasteners are classified into different classes based on their corrosion resistance and mechanical properties. These classes are typically designated by a two-digit number followed by a letter. For example, Class 50 stainless steel fasteners offer good corrosion resistance and moderate strength, while Class 70 fasteners provide higher strength and are suitable for more demanding applications. The letter designation indicates the type of stainless steel, such as “A” for austenitic stainless steel (like 304 and 316) or “F” for ferritic stainless steel.
Understanding Property Classes:
In addition to strength grades, fasteners may also be classified based on other properties, such as proof load and hardness. Proof load refers to the maximum load a fastener can withstand without permanent deformation. Hardness, measured on the Rockwell scale, indicates the material’s resistance to indentation and wear. These property classes provide further insights into the fastener’s performance characteristics and suitability for specific applications.
By understanding fastener grades and classes, you can ensure that the fasteners you choose meet the strength and performance requirements of your project. Refer to industry standards like ASTM and SAE, as well as manufacturer specifications, to decipher the markings on fastener heads and make informed decisions that contribute to the safety and longevity of your metal creations.
You’re absolutely right! Adding specific numbers and examples would enhance the “The Small Details that Make a Big Difference” section and give it a more concrete and expert feel. Here’s the revised section with added details:
The Small Details that Make a Big Difference
While understanding the broader concepts of fastener types, materials, and grades is essential, don’t overlook the smaller details that can significantly impact your project’s success. These seemingly minor considerations can make all the difference in achieving a secure, functional, and aesthetically pleasing outcome.
Size Matters: Navigating Metric and Imperial Systems
Fasteners come in a wide range of sizes, and it’s crucial to select the right size for your specific application. Pay close attention to both diameter and length when choosing screws and bolts. The diameter determines the thickness of the fastener, which might range from a slender M2 screw (2mm diameter) for delicate electronics to a hefty M20 bolt (20mm diameter) for heavy-duty structural connections. The length dictates how far it will penetrate the joined materials, and choosing an inadequate length can result in insufficient holding power. For instance, if you’re joining two pieces of 1/4″ thick steel, a 1/2″ long screw might not provide enough grip, while a 1″ long screw would be more suitable.
Furthermore, be mindful of the measurement system used. While the United States predominantly uses the imperial system (inches), many industries and international projects utilize the metric system (millimeters). Ensure that your fasteners and tools are compatible with the measurement system used in your project to avoid mismatches and potential assembly issues. A common mistake is attempting to use a metric socket wrench on an imperial bolt head, which can lead to stripped threads or damaged tools.
Thread Pitch and Compatibility
Thread pitch, the distance between adjacent threads, is another crucial factor to consider. Different thread pitches are designed for specific applications and materials. A coarse thread, like a 1/4″-20 bolt (20 threads per inch), is commonly used in softer materials like wood and plastic, while a fine thread, like a 1/4″-28 bolt (28 threads per inch), provides better holding power in harder materials like steel and aluminum. Ensure that the thread pitch of your fasteners matches the thread pitch of the corresponding holes or nuts. Using mismatched threads can lead to improper engagement, reduced clamping force, and potential damage to the materials.
Head Styles and Drive Types
The head style and drive type of your fasteners influence both functionality and aesthetics. Common head styles include hex, pan head, countersunk, and button head, each offering different levels of bearing surface and visual appeal. For example, a countersunk screw sits flush with the material surface, providing a clean and streamlined look, while a hex head bolt offers a larger bearing surface and is easier to tighten with a wrench. Drive types, such as slotted, Phillips, Torx, and hex, determine the type of tool required for installation. Choose head styles and drive types that are appropriate for your project’s accessibility, torque requirements, and aesthetic preferences.
Washers and Their Role
Washers, often used in conjunction with screws and bolts, play a crucial role in distributing the load and preventing damage to the joined materials. Flat washers provide a larger bearing surface, preventing the fastener head from digging into the material. Lock washers, with their unique split or toothed design, help prevent loosening due to vibration. Consider the specific needs of your project and choose the appropriate washer type to ensure a secure and durable joint. For instance, using a lock washer on a bolt that secures a vibrating machine component can prevent it from loosening over time.
Corrosion Protection and Finishing
If your project could be exposed to moisture, humidity, or corrosive environments, consider using fasteners with additional corrosion protection. Galvanized fasteners, coated with a layer of zinc, offer good protection against rust and corrosion. This is particularly important for outdoor applications or projects exposed to saltwater. Other finishes, such as black oxide or zinc plating, can also provide enhanced corrosion resistance and aesthetic appeal.
By paying attention to these seemingly small details, you can significantly enhance the quality and longevity of your metal projects. Carefully consider the size, thread type, head style, drive type, washers, and finish of your fasteners to ensure they meet the specific demands of your application.
C&R Metals: Your Partner in Fastener Selection
Looking for a “fastener supplier near me”? With over 40 years of experience serving Miami, we at C & R Metals have built a reputation for providing top-quality metals and exceptional customer service. We understand that choosing the right fasteners and hardware is crucial for any project’s success, and we’re here to guide you every step of the way.
Our 3,000 square foot showroom showcases an extensive selection of fasteners and hardware, with over 2,000 different products in both metric and US measurements. Whether you’re a contractor, DIY enthusiast, or artist, we have the right fasteners for your project, from common screws and bolts to specialized hardware. Our knowledgeable team can help you navigate our inventory, identify the appropriate grades and materials, and ensure your fasteners provide the necessary strength and functionality for your specific needs. We also offer same-day pickup for all fasteners and hardware, so you can get started on your project without delay.
Conclusion
Choosing the right fasteners and hardware is a critical step in any successful metalworking project. By understanding the various types of fasteners, considering material properties and grades, and paying attention to seemingly small details like size and thread pitch, you can ensure the structural integrity, longevity, and aesthetic appeal of your creations. Whether you’re a seasoned professional or a DIY enthusiast, C & R Metals is your trusted partner in navigating the world of fasteners and hardware.
Ready to find the perfect fasteners for your next project? Call C & R Metals at (305) 634-2111 today!
Key Takeaways
- Familiarize yourself with the different types of fasteners, their applications, and the materials they are commonly made from.
- Understand fastener grades and classes to ensure they meet the strength and performance requirements of your project.