Understanding Metal Grades: What You Need to Know Before Buying
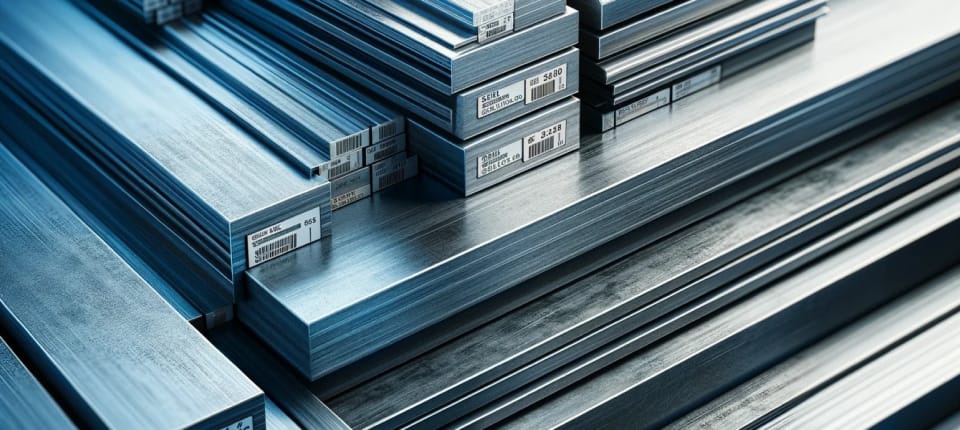
In construction, manufacturing, and fabrication, the success of a project hinges on the quality and suitability of the materials used. Don’t underestimate the importance of understanding metal grades before making a purchase. Metal grades are not merely arbitrary classifications; they are a critical roadmap to a material’s properties, performance potential, and ultimately, its suitability for your specific needs. Failing to grasp the nuances of metal grades can lead to costly mistakes, compromised structural integrity, and project delays. Therefore, it’s essential to arm yourself with the knowledge for confidently navigating the world of metals, making informed purchasing decisions and choosing the right metal for your projects.
What are Metal Grades?
Metal grades serve as a standardized language in the material world, providing a concise way to communicate a metal’s chemical composition, mechanical properties, and intended applications. These grades, represented by alphanumeric designations, categorize metals based on a set of standardized tests and specifications. This ensures consistency and reliability, allowing engineers, fabricators, and builders to select materials with confidence, knowing they will perform as expected. For instance, the SAE steel grades (defined by the Society of Automotive Engineers) utilize a four-digit numbering system to classify different types of steel. Similarly, aluminum alloys are designated by a four-digit number followed by a temper designation, providing insights into their composition and treatment. These standardized systems are essential for maintaining quality control and ensuring that materials meet specific industry standards and regulatory requirements.
Decoding the Grading Systems
Let’s delve into the intricacies of metal grading systems, using steel as our primary example. The SAE steel grades employ a four-digit numbering system that reveals a wealth of information about the steel’s properties.
The first digit indicates the primary alloying element, with “1” representing carbon steel. The second digit generally represents a modification of the primary alloying element or the addition of a secondary alloying element. The last two digits indicate the carbon content in hundredths of a percent. For example, in 1018 steel, “10” signifies plain carbon steel, and “18” indicates a carbon content of 0.18%.
Understanding the role of alloying elements is crucial in deciphering steel grades. Chromium, for instance, enhances corrosion resistance, making stainless steel ideal for harsh environments. Nickel improves toughness and impact resistance, making it a valuable addition in high-strength steels. Molybdenum increases hardenability and creep resistance, making it suitable for high-temperature applications. By understanding these nuances, you can effectively interpret steel grades and select the most appropriate material for your project.
Why Metal Grades Matter
The significance of metal grades extends far beyond mere classification; it directly impacts the success, safety, and cost-effectiveness of your projects. Matching the right metal grade to your project’s specific requirements is paramount. Consider a bridge construction project where high-strength steel with specific yield and tensile strength is necessary to withstand the imposed loads. Using an incorrect grade could compromise the structural integrity and lead to catastrophic consequences.
Consistent performance and reliability are also critical factors. Standardized metal grades ensure that materials meet predetermined specifications, minimizing the risk of unexpected failures or deviations in performance. This is particularly important in industries with stringent quality control requirements, such as aerospace and medical device manufacturing.
Furthermore, metal grades play a crucial role in cost. By understanding the properties associated with different grades, you can avoid over-specifying or under-specifying materials. Over-specifying can lead to unnecessary expenses, while under-specifying can compromise performance and longevity. Selecting the most suitable grade ensures that you achieve the desired balance between cost and performance.
Integrating more specific information about metal grades within each metal type discussion would add significant value and depth to that section. Check out more in the section, which gives expanded details about metal grades.
Metal Types and Their Applications
While understanding metal grades is crucial, it’s equally important to consider the inherent characteristics of different metal types and how specific grades influence their suitability for various applications. This knowledge empowers you to make informed decisions that align with your project’s specific needs and performance expectations.
Steel: The Workhorse of Industry
Steel, an alloy of iron and carbon, stands as the backbone of modern infrastructure and manufacturing. Its versatility, strength, and affordability make it a ubiquitous material in countless applications. Understanding steel grades is paramount when selecting the right steel for your project.
Carbon Steels
These are graded based on their carbon content, which directly influences their strength and hardness. For example, AISI 1018 steel, with 0.18% carbon, is a common mild steel used in general fabrication and structural applications where high strength is not critical. On the other hand, AISI 1045 steel, with 0.45% carbon, offers higher strength and is often used in shafts, axles, and gears. Many carbon steels can undergo further processing to enhance their properties. Cold rolled metal is a prime example of this, where steel is rolled at room temperature to achieve tighter tolerances and smoother surface finishes. This makes it ideal for applications where precision and aesthetics are paramount, such as in automotive body panels, appliances, and furniture.
Alloy Steels
These incorporate various alloying elements to enhance specific properties. For instance, adding chromium creates stainless steels, such as 304 stainless steel (containing approximately 18% chromium), which is widely used in kitchenware and architectural applications due to its excellent corrosion resistance. Adding nickel to steel, as in 316 stainless steel, further enhances corrosion resistance, making it suitable for marine environments and chemical processing equipment. Beyond stainless steels, another crucial category of alloy steels is galvanized steel. This involves coating steel with a layer of zinc to provide superior protection against corrosion, making it ideal for outdoor applications like roofing, fencing, and automotive parts where resistance to the elements is paramount.
Aluminum: Lightweight and Versatile
Aluminum, known for its lightweight nature and corrosion resistance, finds widespread use in industries where weight reduction is paramount. Its high strength-to-weight ratio makes it ideal for aerospace applications, while its corrosion resistance makes it suitable for building facades and marine environments. Aluminum’s excellent thermal conductivity also makes it valuable in heat sinks and cookware.
Wrought Aluminum Alloys
These are designated by a four-digit system, where the first digit indicates the major alloying element. For example, 1xxx series aluminum is essentially pure aluminum with high corrosion resistance, used in electrical applications and chemical storage. The 2xxx series, alloyed with copper, offers high strength and is used in aircraft structures. The 6xxx series, alloyed with magnesium and silicon, provides good formability and weldability, making it suitable for architectural applications and automotive components.
Cast Aluminum Alloys
These are also designated with a four-digit system, but the first digit is followed by a decimal point. These alloys are designed for casting processes and are used in various applications, from engine blocks to decorative castings.
Copper: The Conductor of Choice
Copper’s exceptional electrical conductivity makes it indispensable in electrical wiring, telecommunications, and electronics. Its malleability and ductility allow it to be easily drawn into wires and shaped into intricate components. Copper’s resistance to corrosion also makes it suitable for plumbing and roofing applications.
Electrolytic Tough Pitch (ETP) Copper
This high-purity copper grade (typically 99.9% pure) is widely used in electrical applications due to its excellent conductivity.
Deoxidized Low Phosphorus (DLP) Copper
This grade contains small amounts of phosphorus to improve weldability and is often used in plumbing and heating applications.
Brass and Bronze: Alloys with Aesthetic and Functional Appeal
Brass, an alloy of copper and zinc, is valued for its aesthetic appeal, corrosion resistance, and acoustic properties. It’s commonly used in musical instruments, decorative hardware, and plumbing fixtures. Bronze, an alloy of copper and tin, is known for its durability, wear resistance, and attractive patina. It’s often used in sculptures, medals, and marine hardware.
Brass Grades
Brass grades are often designated by their zinc content. For example, cartridge brass (70% copper, 30% zinc) offers high ductility and is used in ammunition casings. Yellow brass (65% copper, 35% zinc) has a distinctive yellow color and is used in architectural hardware and musical instruments.
Bronze Grades
Phosphor bronze, containing small amounts of phosphorus, offers enhanced wear resistance and is used in bearings and springs Aluminum bronze, with aluminum as the primary alloying element, provides high strength and corrosion resistance, making it suitable for marine applications and pump components.
Titanium: Strength and Biocompatibility
Titanium’s high strength-to-weight ratio, exceptional corrosion resistance, and biocompatibility make it a sought-after material in aerospace, medical implants, and high-performance sporting goods. Its ability to withstand extreme temperatures and harsh environments makes it ideal for applications such as aircraft components, surgical implants, and marine equipment.
Commercially Pure Titanium
This grade is available in four grades (Grade 1 to Grade 4), with increasing strength and impurity levels. Grade 1 is the most ductile and is used in chemical processing and medical implants, while Grade 4 is the strongest and is used in aerospace applications.
Titanium Alloys
These alloys incorporate elements like aluminum, vanadium, and molybdenum to enhance specific properties. Ti-6Al-4V, for example, is a widely used alloy in aerospace and medical implants due to its high strength and biocompatibility. By understanding the unique properties and applications of these different metal types and their respective grades, you can make informed decisions about the best materials for your projects. Consider the specific demands of your application, including strength requirements, environmental conditions, and aesthetic preferences, to guide your selection process.
Making Informed Decisions
Navigating the world of metal grades requires diligence and a proactive approach. Thoroughly research the specific grades required for your project, consulting with experts and engineers when necessary. Don’t hesitate to request material certifications and test reports from suppliers to verify the authenticity and quality of the metals.
Choosing the right supplier is equally crucial. Partner with reputable metal suppliers who prioritize quality, transparency, and clear communication. A reliable supplier will provide detailed information about their metal grades, ensuring that you have a complete understanding of the materials you’re purchasing. C & R Metals, with our commitment to customer satisfaction and expertise in the metal industry, can guide you through the selection process, ensuring you acquire the right metal grades for your specific needs.
Upon receiving your metal materials, conduct thorough inspections to verify markings and certifications, ensuring they align with your project specifications. Address any discrepancies or concerns with your supplier promptly to avoid potential delays or complications down the line.
Conclusion
When selecting metal, understanding metal grades is paramount. It’s not merely a technical detail but a fundamental step towards ensuring project success, structural integrity, and cost-effectiveness. By deciphering the language of metal grades, you gain the power to make informed decisions, choose the right materials for your specific needs, and avoid costly mistakes that can compromise your project’s outcome. Whether you’re working with steel, aluminum, copper, or other metals, recognizing the nuances of their grades is essential for achieving optimal results.
Ready to elevate your metal selection process with expert guidance? Contact C & R Metals at (305) 634-2111 today!
Key Takeaways
- Metal grades provide a standardized system for categorizing metals based on their composition and properties, ensuring consistency and predictability in performance.
- Understanding metal grades empowers you to make informed purchasing decisions, matching the right materials to your project’s specific requirements.
- C & R Metals offers a wealth of knowledge and a wide selection of high-quality metals with proper grading to support your project’s success.